I once bought a CNC machine without thinking much about how it was built. The specs looked solid. The company had decent reviews. And the price? Lower than the competition.
It seemed like a smart buy—until I put it to work.
At first, the issues were small. A missed step here. A rough edge there. Nothing major. But over time, those tiny flaws added up. Cuts weren’t as precise. Production slowed. Repairs piled up. And suddenly, that “good deal” wasn’t so good anymore.
That’s when I realized: not all CNC machines are built the same.
If you’re here, you’re probably asking the same questions I did. How are CNC machines designed, built, and tested?
This guide will break down the entire CNC machine manufacturing process—step by step. By the end, you’ll know exactly how to judge a machine’s quality before you invest.
Let’s begin!
Step#1 Design & Engineering
Before a CNC machine ever cuts its first piece of material, it starts as an idea. Every machine you see in a factory, workshop, or production line was once a sketch on a screen. But turning that sketch into a precision tool takes careful planning, engineering, and real-world testing.
Market Research & Requirements
Manufacturers don’t just build machines and hope they sell. They study the market first.
- What industries need CNC machines?
- What materials will they cut?
- How much automation do buyers expect?
CAD Modeling & Simulation
Once manufacturers know what they’re building, engineers bring the idea to life in 3D.
They use CAD (Computer-Aided Design) software to create detailed digital models. These models include every component—from the frame to the spindle to the smallest screw.
This step is where manufacturers spot potential problems early. Instead of wasting money on faulty prototypes, they test designs virtually.
Stress & Motion Analysis
CNC machines face extreme forces. High-speed spindles generate heat. Cutting metals creates vibration. If the frame flexes too much or the motor overheats, you’ve got a machine that won’t last.
That’s why engineers run virtual stress and motion tests. They simulate:
- How the frame holds up under pressure
- How heat moves through the machine
- How fast-moving parts impact precision
A weak design means inaccurate cuts and constant breakdowns. I’ve seen cheap machines skip this step—and it always shows in their performance.
Prototyping & Refinement
Even the best digital model isn’t enough. Before mass production, manufacturers build a real working prototype.
This is where the design meets reality. Engineers test the prototype, fix weak points, and refine the build. Some companies rush this step to save money. That’s a mistake. A poorly tested machine leads to frustrated buyers and endless repairs.
A good CNC machine starts with careful design, smart engineering, and real-world testing. If a manufacturer cuts corners here, the machine won’t perform when it matters.
Step#2 Material Selection
A CNC machine is only as good as the materials it’s made from. Cheap materials lead to weak machines. Weak machines lead to inaccurate cuts, constant repairs, and wasted money.
I’ve seen CNC machines that looked solid on the outside but fell apart under real production pressure. Bolts loosening. Frames vibrating. Bearings wear out too fast. Most of the time, the problem wasn’t the design—it was the materials.
That’s why material selection matters.
Frame & Structure
The frame is the backbone of any CNC machine. If it flexes, vibrates, or warps, precision is gone.
Manufacturers typically use:
- Cast Iron: Heavy, absorbs vibration, and resists flexing. Great for stability.
- Welded Steel: Lighter but still strong. Works well when reinforced properly.
A poorly built frame leads to rough edges and inconsistent cuts. That’s why serious manufacturers don’t cut corners here. A rigid machine is a precise machine.
Spindle & Linear Components
The spindle, rails, and ball screws handle all the movement. If they wear down, the machine loses accuracy fast.
- Hardened Steel: Used for linear rails and ball screws to reduce wear.
- High-Grade Alloys: Applied to spindles for better durability and heat resistance.
Electronic Components
Electronics power the machine. Low-quality motors and controllers mean jerky movement and positioning errors.
Manufacturers choose:
- Servo Motors: Fast, smooth, and accurate for high-end machines.
- Stepper Motors: More affordable but less precise. Good for hobby use.
- Ball Screws: Minimize backlash and keep movement smooth.
- Trusted Controllers – Control accuracy and software compatibility.
If these parts fail, the whole machine stops. That’s why good manufacturers source from reliable suppliers.
Coolant & Lubrication Systems
Friction wears down parts. Heat damages components. That’s why coolant and lubrication systems are essential.
Manufacturers pick:
- Specialized Fluids: Prevent overheating and extend tool life.
- Sealed Bearings: Reduce maintenance and keep dust out.
Without these, a CNC machine wears out much faster than it should.
The best design in the world means nothing if it’s built with the wrong materials. Strong frames, durable moving parts, quality electronics, and reliable cooling keep a CNC machine running for years.
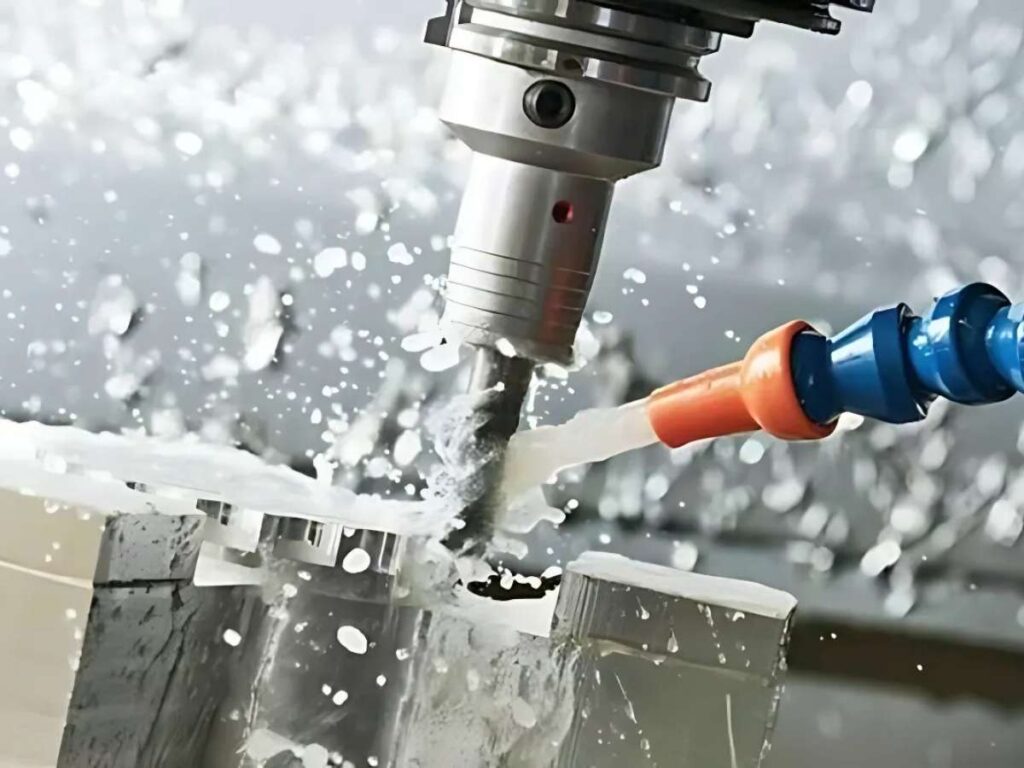
Step#3 Frame & Structural Fabrication
A CNC machine’s frame isn’t just a shell—it’s the foundation. Every cut, every movement, every level of precision depends on it. If the frame isn’t strong and stable, you’ll feel it in every job you run.
I’ve worked with machines where the frame wasn’t built right. At first, everything seemed fine. But over time, the small shifts added up. Cuts weren’t lining up. Vibrations affect precision. Even simple projects took longer because I had to adjust for errors.
That’s why fabrication is a critical step.
Metal Cutting & Shaping
Before the frame comes together, it starts as raw steel plates. These plates are cut into exact shapes to form the base of the machine.
Manufacturers use:
- Laser Cutting: Precise and fast, perfect for detailed cuts.
- Plasma Cutting: Works well for thick steel but isn’t as clean as laser cutting.
- Water Jet Cutting: Uses high-pressure water to cut metal without adding heat.
If these cuts aren’t accurate, alignment issues show up later. A small mistake here can cause headaches down the road.

Welding & Heat Treatment
Once the steel is shaped, it’s welded together. This step determines how well the machine will hold up under stress.
But welding creates tension in the metal. If left untreated, the frame can warp over time, leading to misalignment and accuracy issues. That’s why manufacturers use:
- Stress-Relief Heat Treatment: Slowly heating and cooling the frame to remove built-up tension.
- Annealing: Softens the metal slightly to improve stability.
- Normalizing: Balances internal stress, preventing future shifting.
Some manufacturers skip or rush this step to save time. It might not show up immediately, but over months or years, the frame starts to flex, and accuracy suffers.
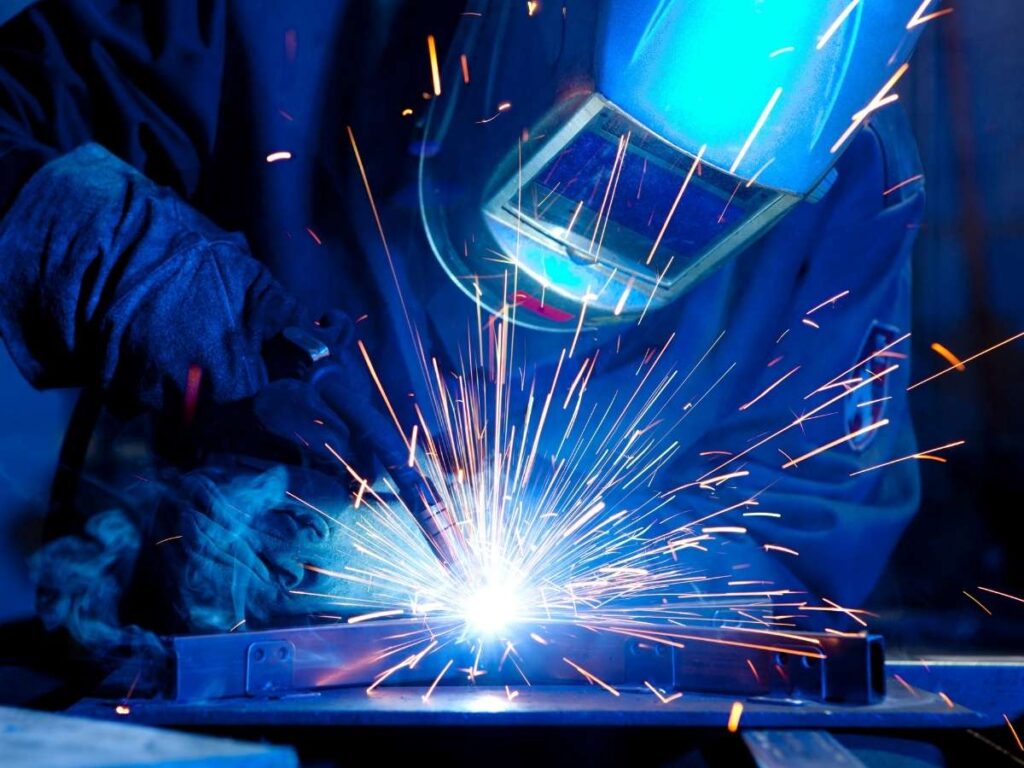
Milling & Surface Grinding
After welding and heat treatment, the frame needs to be fine-tuned. Even the smallest surface unevenness can throw off the entire machine.
To prevent this, manufacturers use:
- CNC Milling: Levels key surfaces so that rails and motors sit perfectly aligned.
- Surface Grinding: Smooths out any imperfections, reducing friction and improving precision.
This step is often overlooked by buyers, but it makes all the difference. A well-machined frame means everything fits together exactly as it should.
A CNC machine’s frame determines its accuracy, durability, and long-term performance. If this step isn’t done right, no amount of fine-tuning can fix it later.
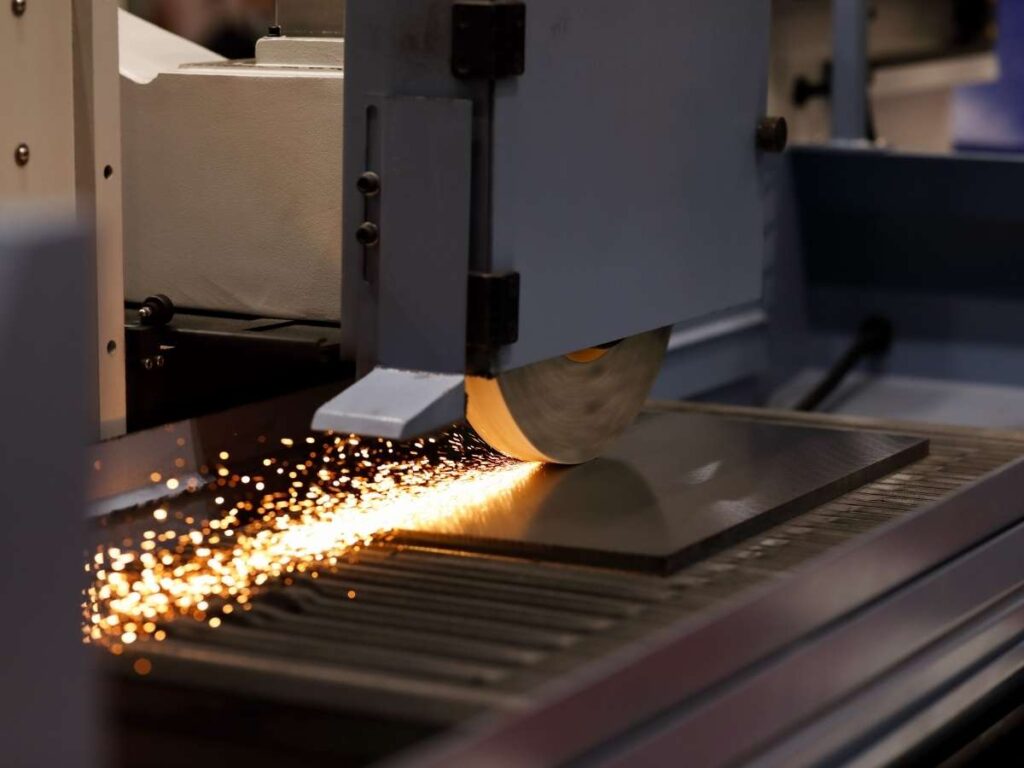
Step#4 Machining of Key Components
A CNC machine is only as precise as the parts that go into it. If one critical component is off—even by a fraction of a millimeter—the entire machine suffers. That’s why machining key parts with extreme accuracy is a step manufacturers can’t afford to rush.
I once worked with a CNC machine that seemed fine at first. But after a few months, I noticed tiny shifts in accuracy. Cuts weren’t lining up. Dimensions were slightly off. It turned out the issue wasn’t wear and tear—it was poor machining on the ball screws and guide rails. Precision starts here. If this step isn’t done right, no amount of calibration can fix it later.
Spindle Manufacturing
The spindle is the most important moving part of a CNC machine. It controls the cutting tool, spinning at thousands of RPMs. If it’s not built with precision, you’ll feel it in every cut.
Manufacturers use:
- CNC lathes to shape the spindle housing with micron-level accuracy (that’s 1/1000th of a millimeter).
- Grinding machines to polish surfaces, reducing friction and increasing lifespan.
A well-made spindle runs smoothly, stays cool under pressure, and maintains precision for years. A poorly made one? It overheats, vibrates, and causes tool chatter that ruins the cut.
Linear Guide Rails & Ball Screws
Ever seen a CNC machine that moves in tiny jerks instead of smooth glides? That’s usually because of low-quality guide rails or ball screws.
To keep motion smooth and accurate, these parts go through:
- Grinding & Polishing: Removes surface imperfections.
- Hardening Treatments: Strengthens the metal so it doesn’t wear down.
- Precision Testing: Ensures they hold positions under heavy loads.
If these components are off by even a hair, cuts won’t be consistent, and long-term accuracy suffers.
Worktable & Fixtures
The worktable might not seem like a big deal—until you try cutting something and realize it’s not perfectly flat. Even a tiny dip in the surface can throw off cuts.
That’s why high-end CNC machines use:
- Aluminum or cast iron tables for durability.
- Machining to ±0.01mm tolerances for perfect flatness.
I once used a machine where the table had slight unevenness. It wasn’t obvious at first, but once I cut parts that needed tight tolerances, the errors started stacking up.
Automatic Tool Changer (ATC) & Bearings
For machines that swap tools automatically, the ATC must be aligned perfectly. If not, tools won’t seat properly, leading to drifting cuts and poor repeatability.
Manufacturers focus on:
- Precision Assembly: To prevent tool misalignment.
- High-Grade Bearings: To keep movements smooth and reliable.
Skipping precision in this step means higher scrap rates, slower production, and constant tool calibration headaches.
A CNC machine is only as good as its weakest component. If any of these key parts aren’t machined with care, the entire machine suffers.
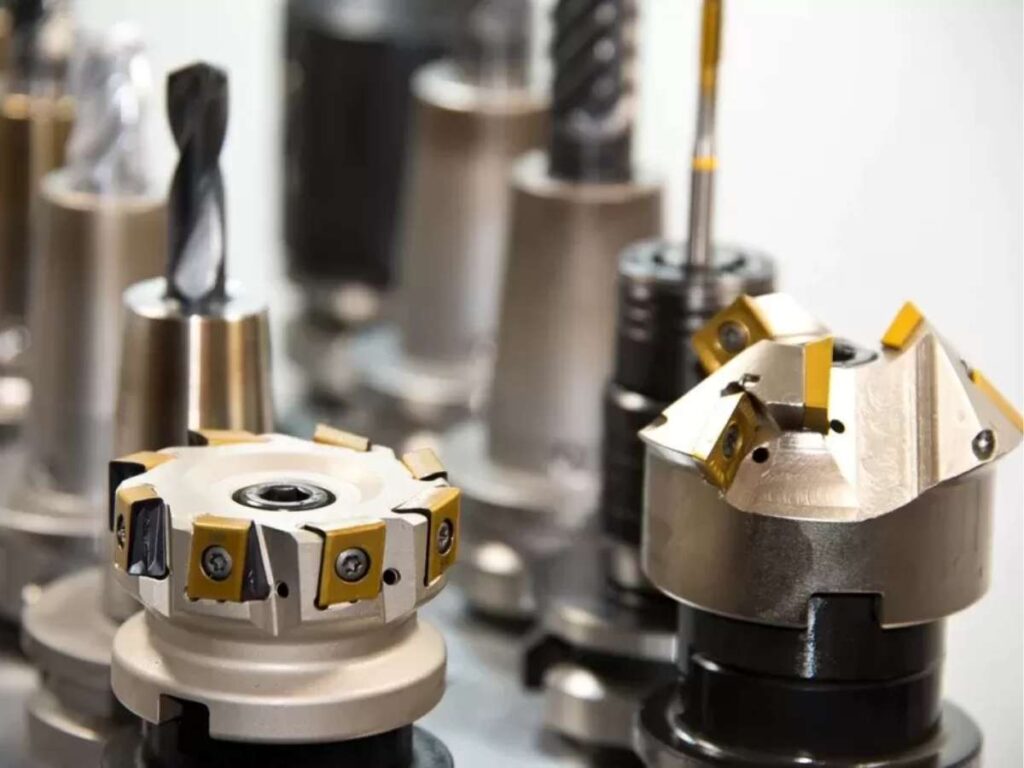
Step#5 Assembly & Integration
This is where everything takes shape. Every bolt, every motor, every moving part must be aligned perfectly. If something is even slightly off, the machine won’t perform the way it should.
Some machines look flawless on the outside but struggle in real production. Often, the problem isn’t the design—it’s how the machine was put together. A misaligned spindle, an uneven frame, or loosely fitted guide rails can cause major accuracy issues down the line. That’s why this step demands precision.
Frame Assembly
The frame is the backbone of the CNC machine. If it isn’t rock solid, everything else suffers.
To ensure stability:
- The machine body is carefully positioned and secured on a level surface.
- Reinforcements are added at key stress points.
- Precision leveling tools are used to eliminate any misalignment.
A frame that isn’t properly squared and leveled leads to constant adjustments, accuracy issues, and frustrating reworks.
In one factory visit, I watched as a technician took extra time adjusting a machine’s base. At first, it seemed excessive. But when the machine was powered up, the difference was obvious. No vibrations. No unnecessary movement. That level of care is what makes a machine reliable for years.
Moving Parts Installation
Once the frame is in place, it’s time to add movement.
At this stage, manufacturers install:
- Ball Screws: These control precise linear motion.
- Guide Rails: Essential for smooth, controlled movement.
- Servo Motors: The driving force behind the machine’s accuracy.
Proper alignment is critical. A slight miscalculation in the ball screws can lead to backlash, where movements become inconsistent. Poorly installed guide rails result in jerky motion that ruins precision.
Spindle Mounting & Tool Holder Setup
The spindle is where real work happens. If it isn’t mounted correctly, vibrations will throw off every cut.
To prevent this:
- Spindles are dynamically balanced to minimize vibration.
- Tool holders are secured with precise torque settings.
- Test runs check for any irregularities before finalizing assembly.
A manufacturer once explained to me why they spend extra time balancing spindles. “If the spindle isn’t stable, nothing else matters,” they said. “You’ll fight bad cuts forever.” That stuck with me. Spindle precision isn’t just about performance—it’s about long-term reliability.
Coolant & Safety Enclosure Installation
Not all CNC machines require coolant, but those that do must have a well-designed system. Poor coolant flow leads to overheating, tool wear, and inconsistent performance.
This step includes:
- Installing coolant tanks and pumps to regulate temperature.
- Adding protective enclosures to keep chips and debris contained.
A CNC machine is only as good as its assembly. Every part must fit together precisely, or even the best-designed machine will fall short.
Step#6 Electronics & Software Integration
A CNC machine is just a pile of metal until the electronics bring it to life. Every movement, every cut, and every tool change starts with a command from the control system. If the wiring is off or the software isn’t set up correctly, the machine won’t perform the way it should.
Controller Installation
The CNC controller is what tells the machine what to do. It processes commands, translates them into movements, and makes sure everything stays on track.
Manufacturers install controllers from trusted brands like:
- FANUC: Used in industrial CNC machines for high precision.
- Siemens: Known for reliability and advanced automation features.
- Mach3 & Mach4 :Popular for hobby and small-business CNC setups.
Each controller is carefully wired to the machine’s motors, sensors, and power systems. If connections are loose or incorrect, the machine won’t function properly.
Motor & Drive Systems
A CNC machine’s movement depends on servo or stepper motors. These motors receive signals from the controller and translate them into precise movements.
- Servo Motors: Faster, more accurate, and better for industrial applications.
- Stepper Motors: More affordable but slightly less precise.
To keep movement smooth, these motors are connected to motion control units that regulate speed, direction, and accuracy. If this step is done incorrectly, the machine may move unpredictably, causing cutting errors.
Wiring & Circuit Board Assembly
Every part of a CNC machine relies on a network of wires, circuit boards, and sensors to function properly.
During this step, manufacturers:
- Install safety switches to prevent machine malfunctions.
- Set up power distribution boards to manage electrical flow.
- Add limit sensors that stop the machine from moving beyond safe boundaries.
If any of these connections are faulty, the machine may shut down unexpectedly or move unpredictably. I’ve heard stories of machines slamming into their limits just because a single sensor wasn’t wired correctly.
Software & User Interface Setup
The software is the bridge between the operator and the machine. This is where tool paths are generated, cutting speeds are set, and machine diagnostics are run.
Manufacturers configure:
- G-Code Processing: The language that tells the machine what to cut.
- Tool Path Generation: Optimizing how the machine moves for efficiency.
- Diagnostic Systems: Monitoring errors and ensuring smooth operation.
Electronics and software turn a CNC machine from a collection of parts into a precision tool. If the wiring is off, the motors aren’t tuned, or the software isn’t configured, even the best machine won’t perform correctly.
Step#7 Calibration & Testing
A CNC machine isn’t ready for production until it proves itself. Even the most well-built machine can have small misalignments, unstable motion, or unexpected issues. That’s why every unit goes through calibration and testing before it reaches the customer.
Skipping or rushing this step leads to machines that fail under real working conditions. I’ve seen companies try to cut corners here, only to deal with returns, complaints, and lost trust. A CNC machine should be flawless the moment it arrives at the shop.
Axis Calibration & Alignment
CNC machines move along multiple axes, and each one must be perfectly aligned. Even the smallest misalignment can lead to inaccurate cuts, uneven edges, or parts that don’t fit together.
To ensure precision, manufacturers use:
- Laser measurement tools to check positioning accuracy down to micrometers.
- Dial indicators to verify movement consistency across the entire work area.
- Compensation software to correct minor deviations.
Once, I tested a machine that seemed perfect at first. But after running a few cuts, I noticed a slight drift on the Y-axis. The issue? A calibration error of just 0.05mm. It may not sound like much, but over multiple cuts, that tiny shift ruined the entire job.
Load & Performance Testing
A CNC machine needs to perform under real conditions. That means testing:
- Spindle RPM :Checking speed stability at different power levels.
- Feed Rate: Ensuring smooth motion without hesitation.
- Torque Response: Making sure the machine can handle resistance without stalling.
Manufacturers push machines through stress tests to check for overheating, vibration, and power fluctuations. If any part struggles, it’s adjusted before final approval.
Sample Cutting & Accuracy Verification
Nothing proves a CNC machine’s accuracy better than an actual cut. Test pieces are made using different materials to verify:
- Surface Finish: The smoother, the better.
- Dimensional Accuracy: Ensuring cuts match programmed measurements exactly.
- Repeatability: Making sure every cut is consistent.
If the test cut doesn’t meet expectations, the machine goes back for adjustments. No unit ships until they deliver precision on every cut.
A CNC machine isn’t just a tool—it’s an investment. Testing ensures that when it arrives, it works exactly as promised.
Step#8 Quality Control & Inspection
A CNC machine might be fully assembled, calibrated, and tested, but it’s not ready to ship yet. Before it reaches a customer, it goes through a final round of inspections. This is where manufacturers catch small issues that could turn into big problems.
Some companies rush this step, eager to get machines out the door. But skipping a thorough inspection leads to costly returns, production delays, and frustrated customers. The best manufacturers take their time to verify precision, safety, and software performance.
Dimensional Accuracy Check
CNC machines are built for precision. If they’re even slightly off, parts won’t fit, and products won’t meet specifications.
To confirm accuracy, engineers use CMM (Coordinate Measuring Machine) tools. These high-precision instruments check:
- Positioning Accuracy: Ensuring the machine moves exactly as programmed.
- Repeatability: Verifying that it makes identical cuts every time.
- Flatness & Squareness :Check that the worktable and axis alignments are perfect.
Safety & Compliance Inspection
A CNC machine isn’t just a cutting tool—it’s a powerful piece of equipment that needs to be safe to operate.
Before shipping, machines go through:
- ISO Certification: Ensures quality and consistency in manufacturing.
- CE Marking: Verifies compliance with European safety regulations.
- UL Testing: Checks electrical safety for North American markets.
A faulty safety switch or an exposed wire can lead to serious risks in a workshop. That’s why these inspections aren’t optional.
I once visited a factory where a batch of machines failed compliance testing due to poor grounding in the electrical wiring. The company had to rework dozens of units, delaying shipments and increasing costs. Catching these issues early saves both time and reputation.
At Blue Elephant, every CNC machine is rigorously tested to meet international safety standards before it reaches your shop. Quality control isn’t just a step—it’s a commitment to safety and reliability.
Software Debugging & Final Adjustments
Even if the hardware is flawless, software issues can still cause problems.
At this stage, engineers:
- Check for G-code execution errors that could cause misalignment.
- Adjust motion parameters for smoother operation.
- Run final diagnostic tests to detect software bugs.
Skipping quality control might save time, but it creates bigger problems later. The best manufacturers take this step seriously, ensuring every machine is accurate, safe, and reliable before it leaves the factory.
Step#9 Packaging & Shipping
Building a CNC machine is one thing. Getting it to the customer in perfect condition is another. These machines are heavy, complex, and full of precision components. One rough trip can throw off calibration, damage wiring, or cause rust before the machine even gets installed.
That’s why proper packaging and shipping are just as important as the build process.
Protective Coating
CNC machines have a lot of metal surfaces. If exposed to moisture, oxidation can begin before the machine is even unboxed.
To prevent this, manufacturers apply:
- Anti-rust sprays on exposed steel components.
- Grease coatings on moving parts to protect against moisture.
- Sealed plastic wrapping to block humidity and dust.
A shop owner once told me about receiving a brand-new CNC machine with surface rust on the ball screws. It wasn’t a huge issue, but it meant extra cleaning and delays. The machine had been stored in a humid warehouse for weeks before shipping. A simple protective coating could have avoided the hassle.
Secure Packing & Crating
Shipping a CNC machine isn’t like shipping a regular package. These machines are heavy, sensitive to impact, and need to be secured properly.
At Blue Elephant, we take extra care to ensure our CNC machines arrive in perfect condition. Every machine is packaged with industry-leading protective measures, including:
- Wooden Crates: Custom-built to prevent movement during transit.
- Vibration-Proof Padding: Absorbs shocks and prevents components from shifting.
- Steel Reinforcements: Used for larger machines that require extra stability.
Some CNC machines are shipped fully assembled, while others come in sections to be put together on-site. It depends on the size of the machine and how easy it is to transport.
Logistics & Customer Support
Once the machine is packed, shipping needs to be carefully coordinated.
Manufacturers:
- Work with trusted freight companies that specialize in heavy machinery.
- Provide tracking updates so customers know when to expect delivery.
- Include installation manuals and troubleshooting guides to help with setup.
- Offer remote support in case customers need assistance after unpacking.
A new CNC machine can be overwhelming, especially for those setting one up for the first time. That’s why many manufacturers offer training videos, user guides, and live support to make the transition smoother.
A CNC machine isn’t just a product—it’s an investment. Protective coatings, strong packaging, and reliable shipping ensure it arrives in perfect condition, ready for production.
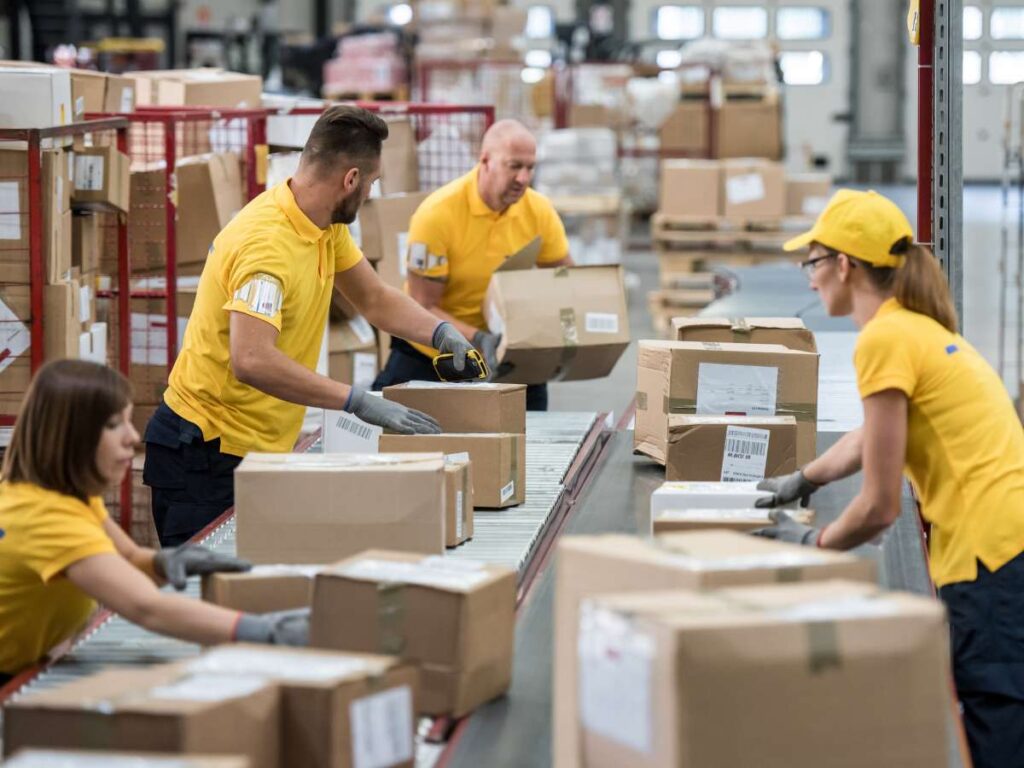
Conclusion
A CNC machine is more than just a tool. It’s an investment in accuracy, efficiency, and reliability. But not all machines are made equal. You’ve seen how small details in design, assembly, and testing can make a big difference.
Now, the question is: Are you ready to choose a machine built for long-term success?
Every great project starts with the right tools. If precision matters to you, don’t settle for less.
Contact us today, and let’s find the perfect fit for your shop.
Explore More Helpful Resources
Want to learn more? Here are some articles filled with valuable tips and information to guide you further:
Still haven’t found what you’re looking for? Don’t hesitate to contact us. We’re available around the clock to assist you.